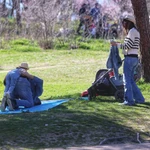
Energía
Una start up usa calor para reciclar aviones
71% se recoge y recicla el 71% del papel usado
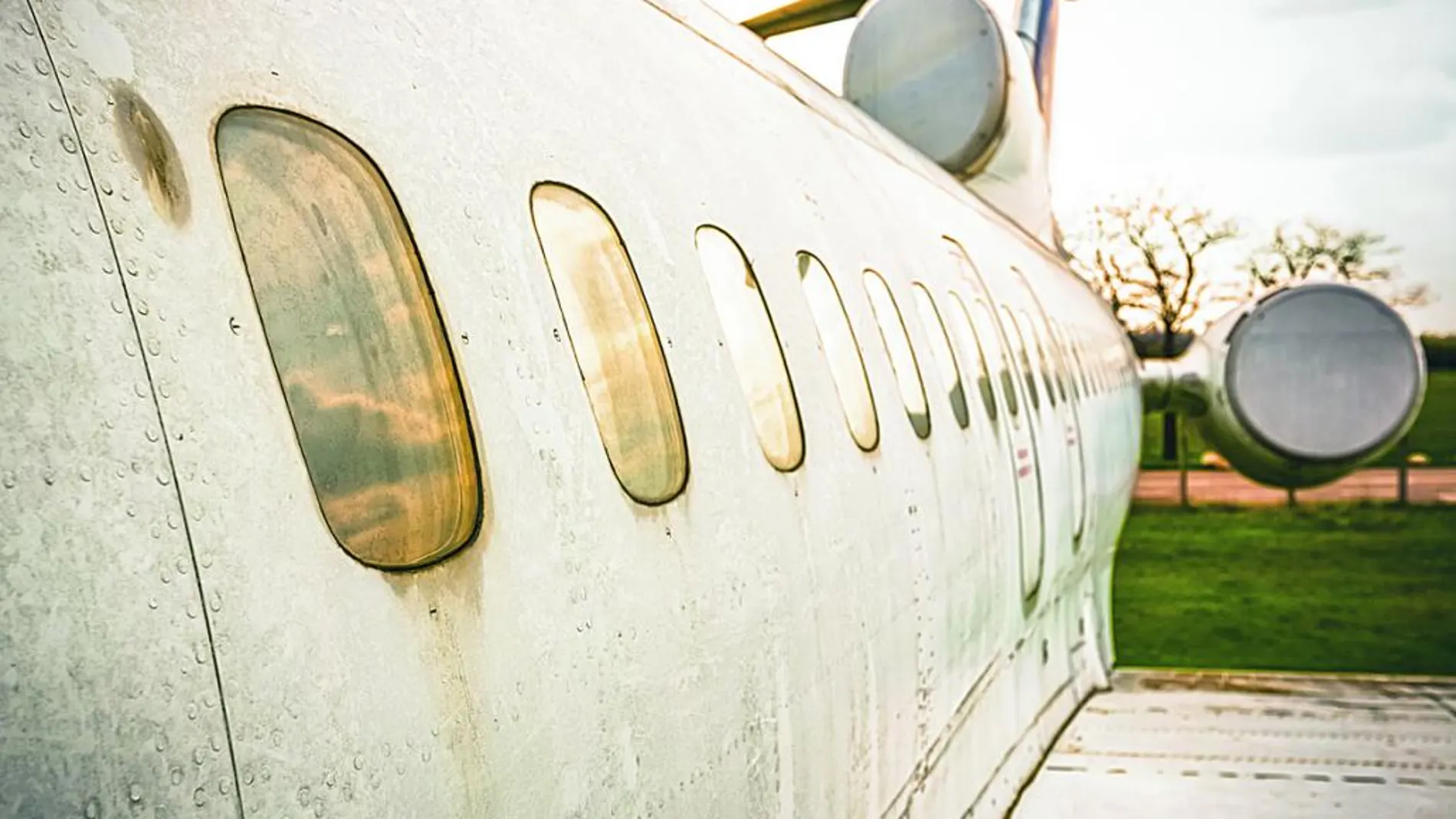
En 2020 se fabricarán 2.000 toneladas de piezas aeronáuticas no reutilizables para las que se buscan soluciones debido a su elevado precio.
Los materiales reforzados o composites son utilizados en multitud de sectores; por sus propiedades son considerados los materiales de construcción del futuro. La demanda de fibra de carbono presentan un crecimiento del 14,9% anual. Y eso que cada año se producen unos 8,8 millones de toneladas de composites (también conocidas como resinas compuestas). Por todo ello, es considerado un residuo emergente», explica Oriol Grau, cofundador de la start-up TRC, una spin-off del CIS que ha desarrollado una herramienta, el R3Fiber, para el reciclado de materiales compuestos reforzados con fibra de vidrio y de carbono. Y es que sólo en el sector eólico, y según datos de Wind Europe, hay aproximadamente 1.800.000 toneladas de residuos (entre ellos palas de aerogeneradores), almacenadas en vertederos de toda Europa. Una cifra que se espera aumente un 40% en los próximos 15 años. «Tenemos datos sobre el sector de aviación que afirman que en 2020 se estima que se producirán 2.000 toneladas de piezas anuales y que para 2035 habrá más de 12.000 aviones desguazados», continúa el emprendedor.
Su proyecto cuenta con el sello de excelencia de la Comisión Europea y ya tienen una planta piloto en la que han probado su tecnología de reaprovechamiento de estas fibras, que son difíciles de reciclar porque vienen impregnadas de resinas. Es por eso por lo que, como mucho, a día de hoy cuando estos materiales caducan (es decir pierden propiedades como su gran resistencia, cosa que sucede tras unos 20 años de uso), se trituran para un posterior uso como aditivos. El resto acaba en vertedero. Un problema que preocupa en sectores como el eólico y el aeronáutico, pero también en el de automoción, donde se está multiplicando el uso de estos materiales (también en modelos eléctricos). Sin embargo, gracias a un técnica térmica, esta joven empresa consigue separar la resina y obtener por un lado, combustible para motores industriales, por otro, gases que se vuelven a introducir en el sistema en forma de energía y por último, las fibras regeneradas. «Las empresas gastan grandes cantidades de dinero sólo en la gestión de este residuo. Se calcula que hasta 3.000 euros por cada pala en el caso del sector eólico. Nosotros recuperamos un residuo que se puede volver a utilizar y con él reducimos el gasto de gestión, calculamos que entre un 5-10%», matiza el emprendedor. Y es que además, el precio de estos materiales nuevos puede alcanzar los 150.000 euros por tonelada en el caso de la fibra de carbono para determinadas piezas o los 6.000 euros por tonelada en el de fibra de vidrio.
Segunda vida
Las nuevas fibras recuperadas conservan su calidad y al menos un 90-95% de propiedades como la resistencia o la ligereza. Esto significa que, de momento, los empresarios no creen que se pueda reciclar un ala de un avión para transformarlo en una nueva pieza estructural, pero sí sirve para crear nuevos componentes como asientos, etc., menos cruciales para la estructura. De esta manera se consigue uno de los efectos más buscados de la industria aeronáutica: reducir el peso de los aviones y con él la necesidad de combustible durante el trayecto.
✕
Accede a tu cuenta para comentar