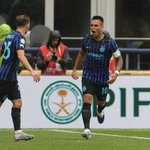
Ingeniería
Reciclan algodón con agua y sal
Un grupo de investigadores de Finlandia propone un sistema para reciclar prendas ya usadas como camisetas utilizando un disolvente orgánico. El proceso, efectivo a bajas temperaturas, representa un paso importante para conseguir fabricar tejido para una población en aumento sin necesidad de ocupar nuevas zonas de cultivo
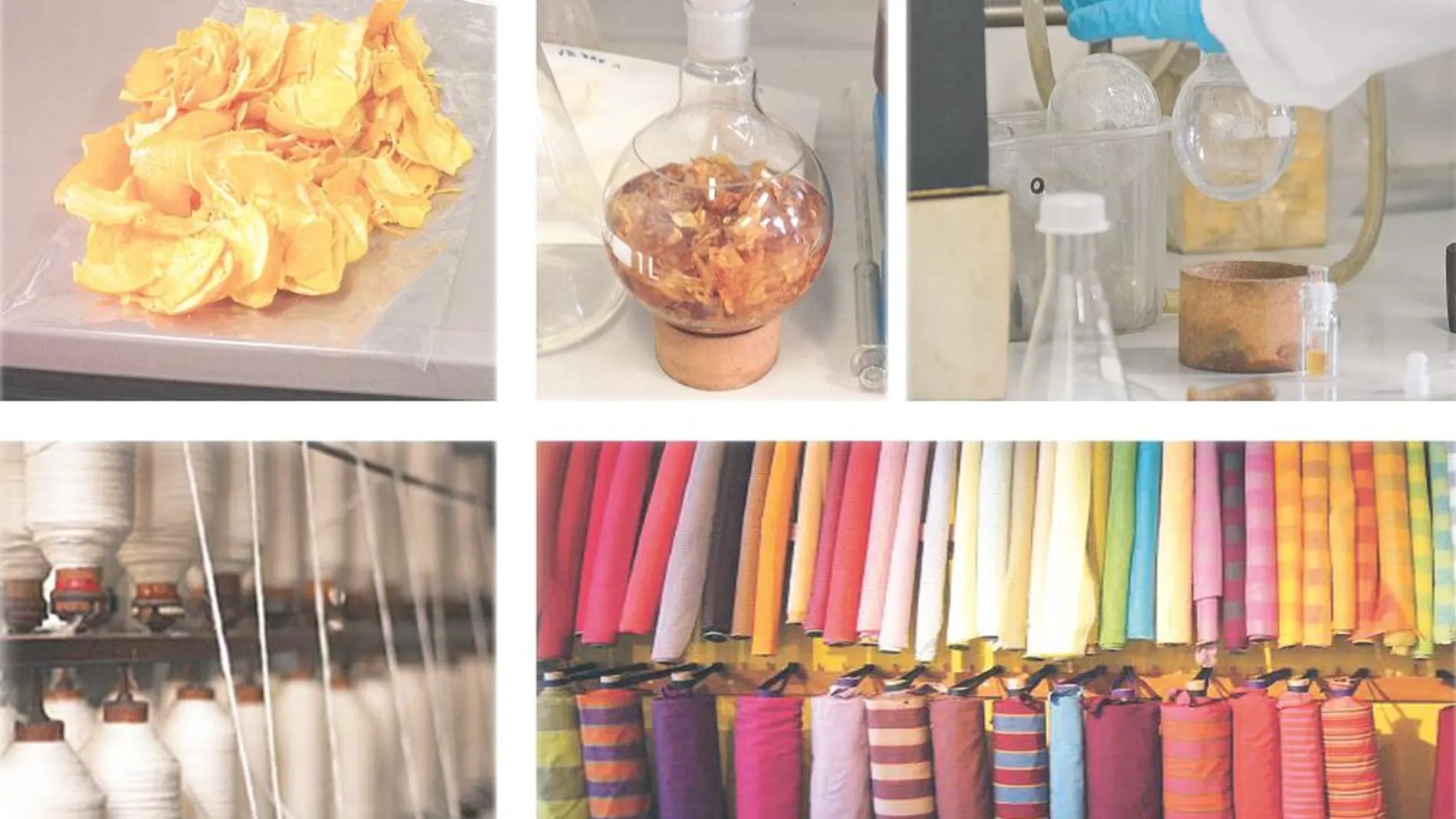
Un grupo de investigadores de Finlandia propone un sistema para reciclar prendas ya usadas como camisetas utilizando un disolvente orgánico
El volumen de producción de fibras textiles se elevó en 2013 un 2,8 por ciento, alcanzando la cifra de 92,3 millones de toneladas de nuevo tejido. De ellos, algo más de 60 millones corresponde a telas hechas de forma industrial, lo que supuso un aumento del seis por ciento respecto al año anterior. Mientras, las fibras naturales descendieron un 2,8 por ciento respecto a 2012, por lo que representan sólo 32 millones de toda esta producción. Este aumento corresponde a un crecimiento de la población y a otro equivalente de las clases medias en las economías emergentes. A esto hay que añadir que está previsto que la población mundial aumente hasta un 20 por ciento en las próximas décadas.
Las celulosas, entre las que destaca el algodón, representan una parte importante del pastel de la industria textil mundial. La producción anual de algodón es de 25 millones de toneladas; sólo en 2013 se produjo un 12 por ciento más que el anterior. La mayor parte de estos tejidos de algodón se producen siguiendo un esquema tradicional. «Se recoge del campo, se empaqueta, se desembala, se abre de forma mecánica con unos motores que consumen mucha energía, se cardan o peinan para dejar el material preparado para su posterior hilatura. Un proceso que consume mucha energía y al que se suma otro intensivo en uso de agua, que se compone de teñido, lavado y secado», explica Manel Lis Arias, investigador de Tecnología Textil Química de la Universidad Politécnica de Cataluña. Se calcula que para producir un kilo de tela de algodón se usan 10.000 litros de agua.
Sin embargo, hace diez años se comenzó a estudiar una tecnología un poco menos intensiva en el uso de agua y energía. Es lo que se conoce como proceso Lyocell, aunque a día de hoy representa una pequeña porción en la industria del tejido de algodón ecológico. De hecho, en 2014 sólo 0,22 millones de toneladas de estos productos eco se hicieron siguiendo esta técnica, frente a los 4,6 millones que se fabricaron con esta proporción de consumo de agua antes explicado. Este proceso de hilatura, llamado Lyocell, está industrializado desde hace sólo cinco años; existen algunas fábricas en Estados Unidos, Austria e Inglaterra. El proceso es bastante sencillo: «la celulosa tiene una estructura muy compleja. Para eliminar los componentes que no son útiles se introduce en un disolvente químico que los separa. Al quitar este disolvente, la celulosa vuelve a estructurarse en filamento y tejido», explica LIs. Las dos ventajas que tiene este proceso relativamente nuevo son: por un lado se recupera todo el disolvente ya que el proceso se realiza en un circuito cerrado y sellado. Y, por otro, se consume mucha menos agua. «Con este técnica se necesitarían sólo 500 litros de agua que se recicla constantemente», explica Alice Beyer Schuch, diseñadora de prendas de algodón reciclado.
Con una población siempre en aumento, los procesos que utilicen menos agua se hacen importantes, como también lo son aquellos que reciclen liberando tierra necesaria para los cultivos de alimentos. «Actualmente alrededor del tres por ciento de la tierra del mundo se utiliza para cultivo de algodón», explica Alice. Y lo más sorprendente es que aunque exista una tecnología como Lyocell algo menos agresiva medioambientalmente, hasta ahora no existe ningún proceso industrializado que fabrique fibra de algodón totalmente reciclado. «Los desechos de camisetas o vaqueros van a parar a mercados de segunda mano o se venden a África, pero sólo un parte muy pequeña, entre un uno y un 2,5 por ciento se rasgan de manera mecánica y se incorporan al proceso de fabricación tradicional. Hay algún proyecto que intenta no usar cien por cien algodón nuevo sino una parte de residuos de camisetas, pero en los procesos tradicionales intensivos en el consumo de agua y energía. A día de hoy no hay ninguna fábrica Lyocell que utilice algodón reciclado», matiza Lis.
Un paso más
Beyer explica que hay algunas empresas, como Re:new el o SaxCell, que están intentando lograr semejante hazaña de forma industrial. De hecho una de ellas quiere abrir la primera fábrica este mismo año. A ellas se suma una propuesta de la Universidad de Finlandia que acaba de ganar el primer concurso organizado por H&M Global Change Award. El equipo de investigadores de Michael Hummel propone convertir los residuos de algodón en nuevo tejido, utilizando un proceso igual al del Lyocell, pero con una enorme diferencia: en lugar de líquidos tóxicos para deshacer el algodón, hacen uso de un disolvente orgánico. «La diferencia principal entre el proceso lyocell y el proceso Ioncell-F desarrollado por Finlandia está en el disolvente utilizado, que no es más que una sal como la que se usa en casa para cocinar», explica Beyer, quien ha trabajado con el equipo finlandés y conoce de primera mano este proyecto. Durante sus investigaciones, los universitarios testaron su disolvente con las sábanas de un hospital público, obteniendo nuevo hilo, del que afirman que es más resistente que otras fibras comerciales. «La ventaja que tiene la celulosa es que al regenerarla se le pueden dar propiedades nuevas», matiza Lis.
Otra ventaja, además del reducido consumo de agua -puesto que el proceso se basa en Lyocell-, es la necesidad de energía, ya que su disolución actúa a menos de cien grados de temperatura. «Este proceso posibilita utilizar otros materiales, aparte de la madera, para la producción de fibras regeneradas (o artificiales). Se puede pensar en utilizar papel (los hilos marrones están hechos con papel reciclado y cartón), telas de algodón, pero también telas de lino e, incluso, residuos de plantas», afirma Beyer.
La fundación de la marca H&M propuso esta idea en verano de 2015 con la intención de que los emprendedores que quisieran registraran sus ideas innovadoras sobre tejidos, procesos de fabricación más sostenible y economía circular. Hasta finales de octubre se recibieron un total de 2.700 proyectos de 112 países. De ahí se pasó a la votación popular y a la elección de los cinco finalistas, que se han repartido un millón de euros y están disfrutando de un programa de aceleración y coaching. La innovación ganadora se ha llevado 300.000 euros de premio, aunque no es la única, ya que la cuantía de esta primera convocatoria ha sido de un millón de euros.
La segunda finalista es una idea que viene de EE UU y que tiene que ver con el reciclado de poliéster. Para ello proponen cambiar el procedimiento industrial por el uso de microbios que realicen la misma función. Es decir que asimilen el tejido y los transformen en nuevo hilo de forma natural a través de su aparato digestivo. Hay que recordar que a diferencia del algodón, el poliéster ya se recicla porque es sintético, se conoce su estructura y es fácil de separar. Además no necesita disolvente.
Juegan también con la idea de economía circular otros dos de los finalistas. La start up Orange Fiber trabaja desde hace tres años, junto a la Universidad de Milán, en el transformación de los residuos de la industria de zumo de naranja en un nuevo tejido incoloro. Por el momento han conseguido darle salida unas pocas toneladas de la cáscara proveniente del millón de naranjas que se producen en Italia anualmente. Desde Holanda proponen también la utilización de algas para crear nuevo tejido industrial. Nuevos residuos que van ocupando un mayor espacio en los escaparates. Sólo hay que recordar las colecciones que reutilizan basura proveniente del mar, etc.
«Las grandes marcas, como en este caso H&M saben que éste es el camino, porque no hay plan B. Por eso apuestan por encontrar opciones y si se consigue reciclar algodón estará fenomenal. Otra cosa es que su modelo de negocio vaya a ser sostenible, ya que está basado en la venta masiva», afirma Gema Gómez, directora de Slow Fashion España.
✕
Accede a tu cuenta para comentar