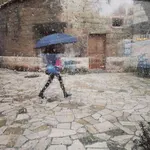
Ciencia y Tecnología
Crean un sistema para predecir las averías en los aerogeneradores
De una experiencia en buques, logran desarrollar un sistema inteligente para saber el estado en el que se encuentra cada parte de las instalaciones eólicas
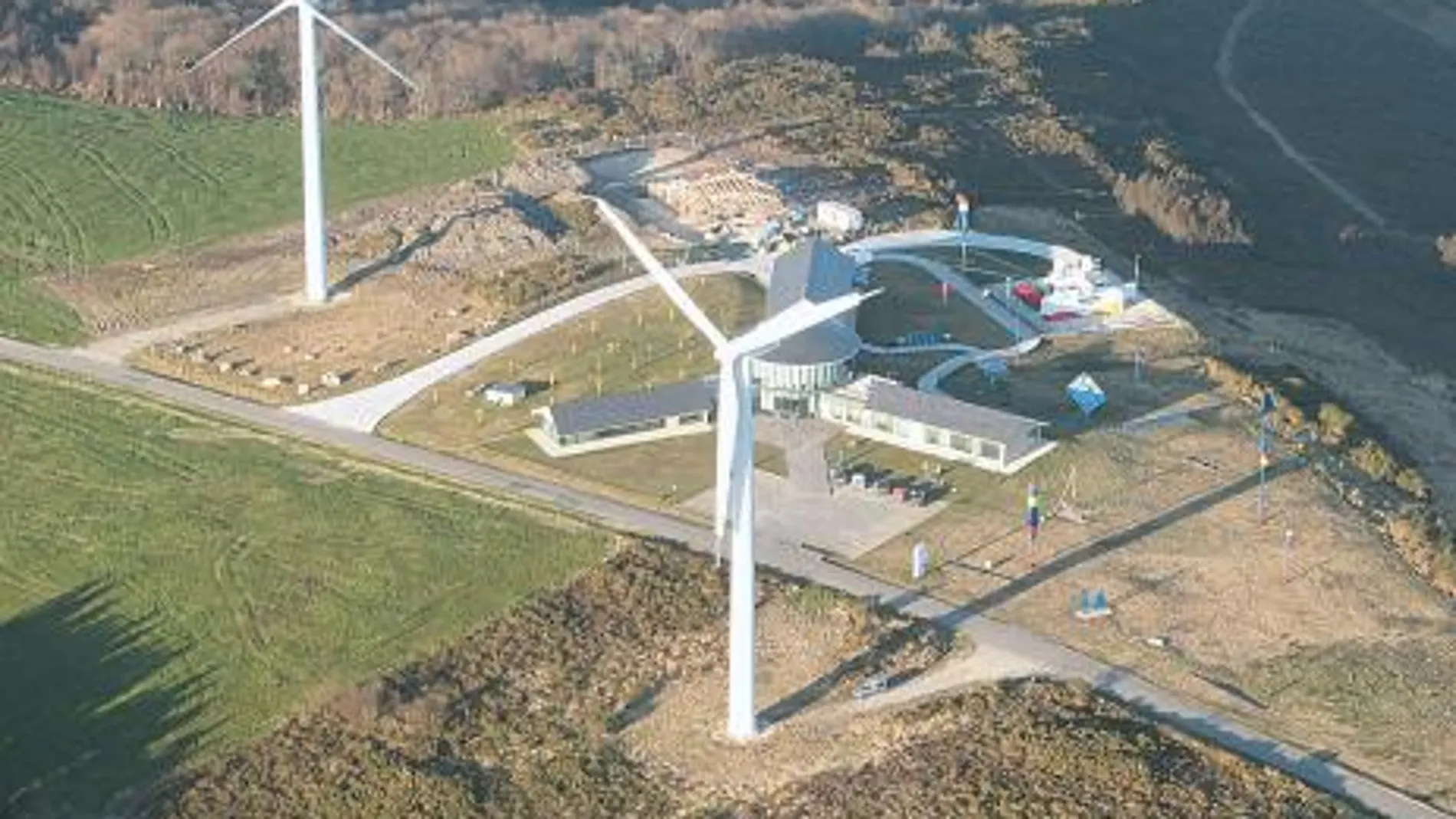
Mientras se desarrolla el debate sobre la energía nuclear, las innovaciones tecnológicas prosiguen en el campo de las renovables. La Universidad de La Coruña y la empresa española Indra están inmersas en sacar adelante el prototipo Aerogidas, con el que pretenden desarrollar un sistema de mantenimiento inteligente para aerogeneradores eólicos. Así será posible conocer, con cierta antelación, posibles fallos que se puedan dar en la máquina, sea cual fuere su lugar de origen y sustituirlo con la mayor brevedad posible. El prototipo se está probando en el Parque Experimental de Sotavento. Las diferentes tecnologías implantadas en el sistema intentan predecir, a partir de unas variables como las vibraciones o el sonido, el posible fallo en el sistema. Unos sensores en las carcasas de los aerogeneradores dan la información respecto de cuál es el estado de las piezas mecánicas. La planta recoge y procesa los datos y la información se envía a un centro de control que visualiza las señales y las gestiona para poder predecir.«Lo principal es conocer de antemano la salud de un aerogenerador», dice Pablo Segovia, responsable del proyecto por parte de Indra. «El sistema permite poder monitorizar, detectar averías y predecir qué es lo que ocurre con ella», indica Amparo Alonso, catedrática en las Áreas de Ciencias de la Computación e Inteligencia Artificial de la Universidad de La Coruña. Menos gastoEl hecho de predecir los fallos con más antelación conlleva beneficios como la reducción del coste de mantenimiento y de operación del sistema. Además, se produce un aumento en la disponibilidad operativa mientras que se prolonga el ciclo de vida del aerogenerador. Otro hecho clave es que permite la supervisión remota de los componentes que controla. Por último, destaca la capacidad de predicción. El proceso que sigue es que en el momento en el que el sistema detecta que un componente mecánico está fallando avisa a los responsables de mantenimiento. Éstos piden a la fábrica las piezas, lo cual supone «un ahorro en stocks y el tiempo de espera en recibir el componente», explica la responsable por parte de la Universidad. La experiencia piloto, denominada Gidas, se ha aplicado en los motores de los buques de la Armada. «El sistema se compone de un hardware que captura los datos que crea los parámetros y un software que analiza toda la información», explica Segovia. Se ha llevado al campo de las renovables y se planea que en un futuro se aplique en otras áreas, ya que «una vez hecha la experiencia vimos que los resultados se podían trasladar a otras áreas», dice Amparo Alonso. Hasta ahora el principal problema es cuando tienes que sustituir alguna pieza. Si no dispones de ellas, hay que esperar a recibirlas de los proveedores, lo cual conlleva en ocasiones tener que cerrar el parque. «Por ejemplo, el de Sotavento, donde estamos haciendo los experimentos, tuvo un problema y hubo que cerrarlo durante unos seis meses», explica Amparo. Las energías renovables se encuentran en pleno crecimiento, pero existe «poca información estandarizada y no hay homogeneidad en las especificaciones», aclara Amparo.En la actualidad se está prediciendo el error con un margen de aproximadamente un mes, cifra que se pretende aumentar. «Ahora intentamos que ese tiempo sea mayor, obviamente, con la fiabilidad de la previsión», finaliza la catedrática.
✕
Accede a tu cuenta para comentar