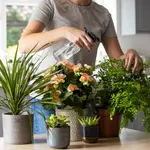
Ingeniería
El fin del ladrillo
Estructuras urbanas menos invasivas visualmente, más resistentes y que no necesitan mantenimiento. Es el futuro de la construcción que, gracias a los materiales compuestos, se está convirtiendo en presente. Las fibras y los plásticos sustituyen al hormigón y al acero en los cimientos de unas obras civiles cada vez más sostenibles

Desde hace unos años los materiales compuestos o «composites» (palabra anglosajona que ha desbancado a su traducción española) están desplazando al hormigón en las grandes obras de ingeniería civil. A pesar de que el coste de estos materiales es superior, las ventajas que ofrecen tanto a nivel mecánico como de mantenimiento los han convertido en un complemento para los diseños más caprichosos. Pero ¿cuál es el secreto de los composites? Como su nombre indica, son materiales formados por varios elementos. «Son dos materiales diferentes y reconocibles, a diferencia de lo que ocurre en las aleaciones», explica José Ygnacio Pastor, catedrático del departamento de Ciencias de los Materiales de la Universidad Politécnica de Madrid. Materiales típicos del sector aeronáutico, como los polímeros o plásticos, fibras de vidrio y de carbono, dan el salto desde los aviones a la construcción de edificios, puentes y pasarelas, entre otros muchos usos. Nadie duda de que son el futuro de la construcción sostenible y suponen a día de hoy una revolución comparable a la máquina de vapor en el sector de los transportes. «Va a ser una revolución silenciosa», en palabras de Pastor, que destaca que los actuales Códigos Técnicos de la Edificación van a normalizar esta modernización, necesaria pero que ha encontrado cierta resistencia hasta el momento por los bajos costes del ladrillo y el hormigón.
Un centro especializado
Desde el Centro Tecnológico de I+D+i de Acciona en Madrid, unos 160 profesionales trabajan desde hace más de una década en hallar soluciones modernas a las necesidades constructivas. Una de las especialidades de este gran laboratorio son los «composites». Fruto de proyectos de investigación como el Prometeo, finalizado en 2009, nacen las aplicaciones y diseños de diversos puentes y pasarelas peatonales que la empresa está diseñando y construyendo por todo el país. A través del trabajo de los ocho laboratorios del centro, se da continuidad al objetivo de este proyecto del Cenit (programa de apoyo al I+D+i, gestionado por el Centro de Desarrollo Tecnológico Industrial, adscrito al Ministerio de Ciencia e Innovación): facilitar la transición de la construcción en acero y hormigón a otra más moderna y energéticamente eficiente. «Llevamos trabajando en obra civil con los "composites"desde mediados de los 90. Para este año tenemos prevista la construcción de tres pasarelas peatonales en Madrid, Cuenca y la isla de La Palma respectivamente», explica José Daniel García Espinel, director del departamento de Implantación e Innovación del Centro Tecnológico de Acciona en Madrid. En estos años, los resultados se pueden ver repartidos por la geografía española, en estructuras ligeras y grandes vanos de luz, con menos impacto visual y formas caprichosas.
Aquí se fabrican los laminados de fibra, normalmente de vidrio o de carbono (aunque se pueden combinar), con una determinada orientación, es decir, con una dirección concreta. Varias capas de estos laminados configuran una pieza. En el sistema más común para la fabricación de estos laminados, llamado de infusión, las telas se extienden y se compactan a través de la aplicación de vacío. Ayudadas por una «bolsa» de plástico, dos válvulas van dejando pasar la resina (que actuará de pegamento) y le van quitando el aire. Las placas resultantes tienen diferentes espesores en función de las necesidades estructurales de la obra y de su colocación. Cuando se necesitan laminados especialmente gruesos, una forma de ahorrar en espesor y en material (si, por ejemplo, fuéramos a emplear una tela de un centímetro de fibra de carbono) es hacer un sándwich. Se trata de unir dos placas más finas añadiendo en su interior un relleno de poliuretano.
De cada laminado o sándwich se sacan muestras o «probetas», con los cortes y características que indique la normativa para exponerlas a diferentes esfuerzos: de tracción, para ver hasta dónde se alarga sin romperse; de flexibilidad, hasta dónde es aceptable que se estire sin que se deforme, etcétera.
Estructuras caprichosas
Características como su ligereza, maleabilidad y el que no sufra la corrosión los hacen interesantes para diferentes tipos de construcciones. Por ejemplo, en depuradoras o depósitos de aguas corrosivas, ya que «en el hormigón siempre hay filtraciones», señala Andrés Viñolo Albione, jefe subárea de Innovación de la Dirección de Investigación, Desarrollo e Innovación de Acciona. Otro de los usos llamativos es en la construcción de estaciones de metro. Pueden sustituir a las barras de hierro que marcan y aseguran el perímetro antes de que pase la tuneladora, con la ventaja de que van desapareciendo según pasa la máquina. Algo que las barras de hierro no permiten, ya que provocarían que la tuneladora se atascara. Literalmente es como si se comiera las barras de composite, en este caso, de fibra de vidrio.
Para puentes y pasarelas peatonales, la ventaja, además de que el mantenimiento posterior con pintura antióxido desaparece, es que permite eliminar puntos de apoyo sin aumentar el canto del tablero. O lo que es lo mismo, la luz o distancia entre apoyo de vigas es mayor, ya que el peso es menor. «Un puente en fibra puede pesar unos 12.000 kg.
En hierro ese mismo puente llegaría a los 40.000 kg», detalla Viñolo. Todo un juego mecánico de pesos.
Además, se puede construir toda una estructura en laboratorio, trasladarla y montarla de una pieza en el lugar de la obra. Es lo que ocurre en una de las pasarelas que Acciona está preparando para su instalación en los próximos meses. Pensada para la isla de La Palma (Canarias), para el centro urbano de Los Sauces, el paso peatonal diseñado tiene que responder a las particulares necesidades urbanísticas de la zona. Se trata de una estructura de 23,34 metros de luz y una altura de 1,10 metros. La elección en materiales compuestas supone una disminución de 10 veces menos respecto a otros materiales tradicionales como el hormigón. La ligereza es fundamental en este tipo de obras urbanas. «A pesar de su elevado precio inicial, pueden reducir los costes, ya que disminuye los plazos de ejecución de la obra. Su escasa conductividad térmica puede ayudar a las construcciones a ser más sostenibles; dan lugar a fachadas que aíslan mejor», detalla Pastor.
✕
Accede a tu cuenta para comentar