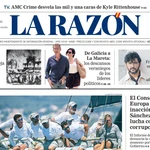
Transición energética
Hidrógeno verde y biogás para fabricar un pladur bajo en emisiones
La fábrica de Pladur de Valdemoro, la más grande de Europa, consumirá a primeros de 2024 al menos un 10% de hidrógeno renovable en lugar de gas natural
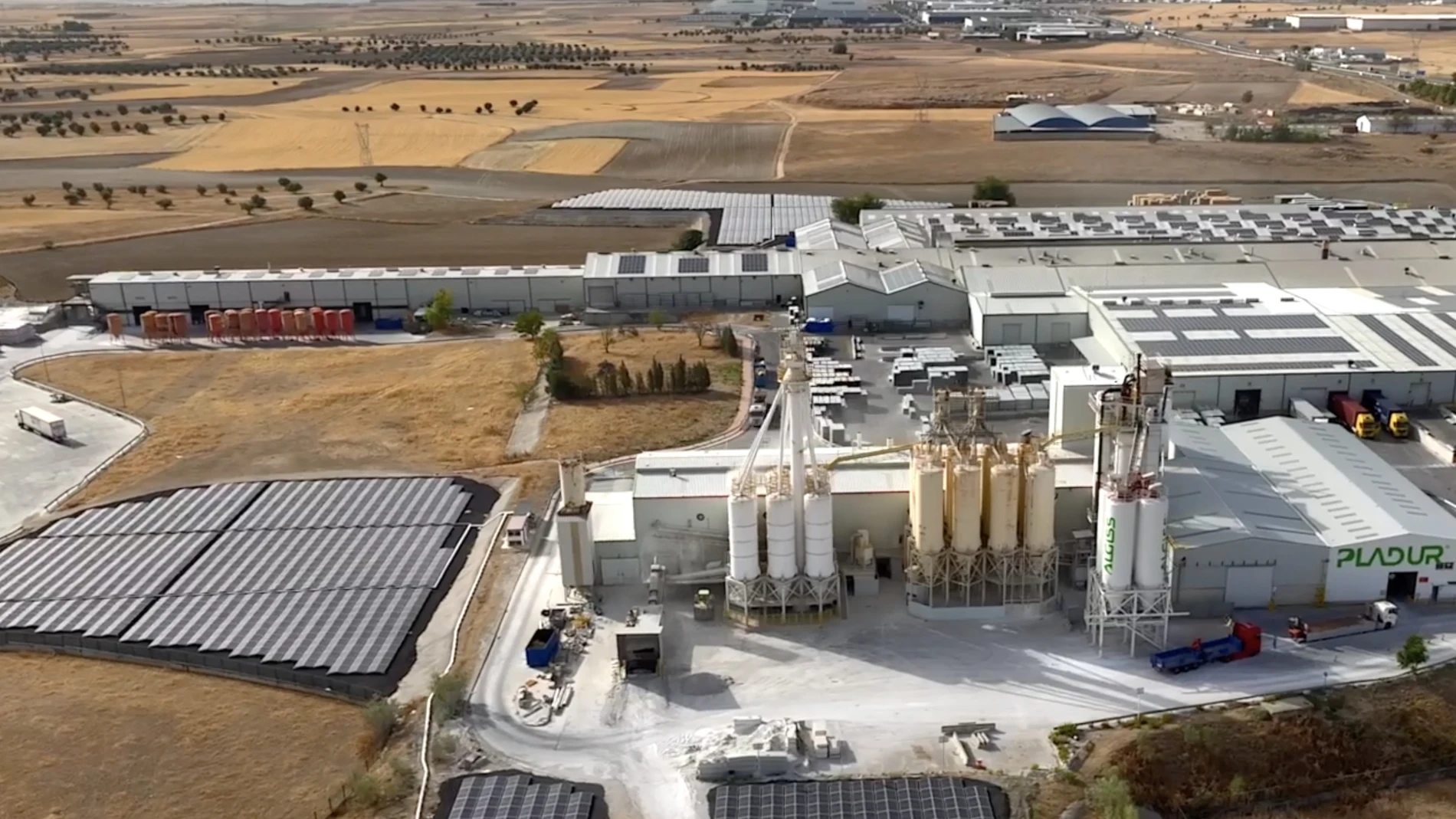
Celulosa y yeso. Son los materiales básicos para construir una placa de yeso laminado, un material de construcción que se inventó a finales de los 70 y que es mucho más conocido por el nombre de la marca que lo inventó. Pladur comenzó su negocio en 1978 y actualmente solo de su planta de Valdemoro (Madrid) salen cada hora 70 toneladas de estas placas, todo el material necesario, dicen aquí, para construir 400 viviendas. Hay que aclarar que esta fábrica es el buque insignia de la compañía, la planta más grande de Europa y la principal en España de las cinco que tiene en la Península (Girona, Jaén, Zaragoza y Navarra).
Aquí se hace todo el proceso de fabricación desde la pasta a la perfilería y la placa. El yeso, o como aquí lo llaman el oro blanco, es la primera materia que se necesita para fabricar una placa laminada. El mineral se extrae de las canteras de la firma y una vez en la planta se somete a varios procesos de triturado, molienda y calcinación. Se obtiene entonces un polvo que será trabajado junto a otros materiales como el cartón hasta obtener las famosas placas de pladur.
La fabricación de pladur es gas intensiva, es decir, consume gran cantidad de gas natural. «El consumo de combustible y las emisiones de esta industria provienen principalmente de dos procesos: del triturado y la molienda del mineral y posteriormente del secado de las placas laminadas, donde se puede llegar a consumir hasta un 40% del gas de toda la planta», detalla Emilio Gómez, director de la fábrica.
Hay que recordar que la descarbonización no es solo el gran objetivo de esta fábrica, sino de todo el sector de la construcción. Esta industria representa el 34% de la demanda de energía a nivel mundial y el 37% de las emisiones según el Informe sobre la situación mundial de los edificios y la construcción de 2022 que se presentó en la pasada Cumbre del Clima (COP27).
Para minimizar emisiones, Pladur se ha decidido por varias vías.
La primera es la instalación de paneles solares en cubierta y el desarrollo de un huerto solar. Actualmente cuentan con unos 12.000 módulos instalados con los que cubren en autoconsumo un 38% de la electricidad que necesitan para fabricar las 24 horas del día. Sin embargo, su gran reto es sustituir el gas natural. ¿Cómo? Apostando por fuentes de energía alternativas como el hidrógeno o el biometano. Para finales de este año o primeros de 2024 Pladur quiere que en esta planta se consuma al menos un 10% de hidrógeno verde en lugar de gas natural. También quieren probar a inyectar en sus hornos biogás aunque eso ya será más a medio plazo. El reto no es baladí sobre todo en sobrecostes. Y es que, al menos de momento, el precio del hidrógeno verde es más alto que el del gas natural por mucho que este último haya subido desde el estallido de la guerra en Ucrania. «En enero del año pasado el precio del gas natural rondaba los 20 euros el MWh. En agosto de ese mismo año alcanzaba los 320 euros. Se encareció más de diez veces y eso ha tenido un impacto brutal en nuestra industria», cuenta el director general de Pladur, Enrique Ramírez.
El hecho de que Europa se haya fijado objetivos de reducción de emisiones en el sector de la construcción y objetivos de rehabilitación energética de edificios se ve aquí como una buena oportunidad para este material, que sigue comiéndole terreno, dice Ramírez, a otros sistemas de construcción más tradicionales como el ladrillo y el mortero. «Si queremos llegar al 2030 con una economía descarbonizada, hay que rehabilitar unas 22 millones de viviendas y hay que recordar que el yeso durante su fabricación, emite entre 4 y 5 veces menos que materiales como el ladrillo. Nuestras temperaturas de secado son de 130-150 grados, pero cualquier cerámica tiene que secar por encima de los mil grados. Además, el pladur es eternamente reciclable, permite la construcción modular y tiene buenas propiedades como aislante térmico o acústico», continúa el directivo.
El agua es otro de los grandes consumos de la fábrica. «Se utiliza para obtener la pasta de yeso, con la que se rellenan las láminas de cartón y se producen las placas», dicen desde la firma. Para minimizar su consumo, la planta de Valdemoro cuenta con colectores de lluvia. Además, se está dando forma a un acuerdo con el Canal de Isabel II y el ayuntamiento de Ciempozuelos para utilizar solo agua reciclada durante el proceso. También se le ha declarado la guerra al plástico. Solo en un año han reducido un 50% su uso en embalajes gracias a dos sencillas acciones. reduciendo el gramaje del material que utilizan y realizando perforaciones en sitios estratégicos de los paquetes de placas.
Sin residuos
En 2008, Pladur abrió la primera planta de reciclaje de yeso y desde entonces todo lo que sobra durante la fabricación se vuelve a introducir en el proceso. Ahora el reto es conseguir que el reciclado llegue a pie de obra. «Para ello hemos solicitado a la administración convertirnos en gestores de residuos. España no está avanzada en la segregación de residuos en obra, pero el objetivo de Europa es que algún día obtengamos todo lo que necesitemos de los edificios, que se convertirán en bancos de materiales», concluye Ramírez.
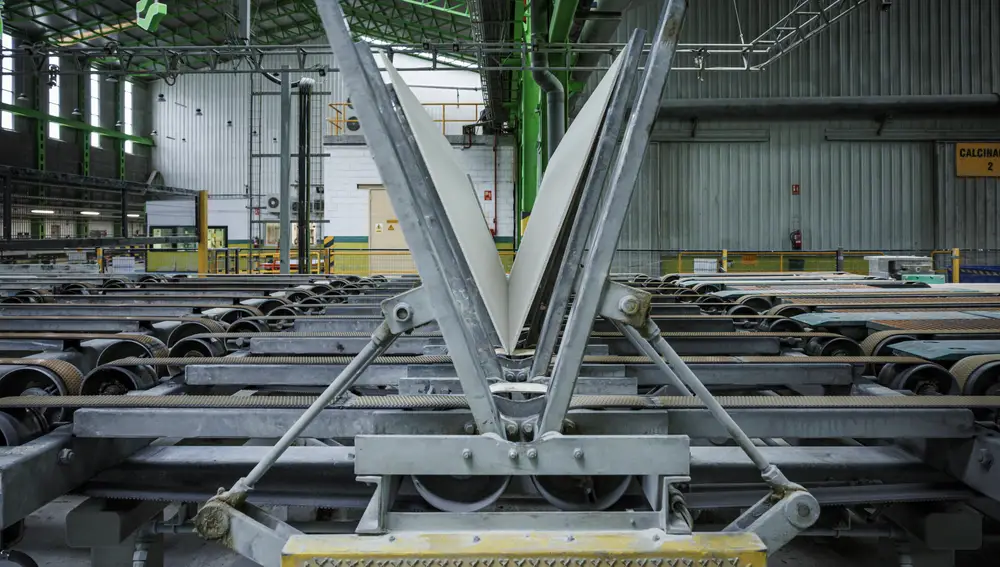
✕
Accede a tu cuenta para comentar